Can you predict and identify failure before it happens?
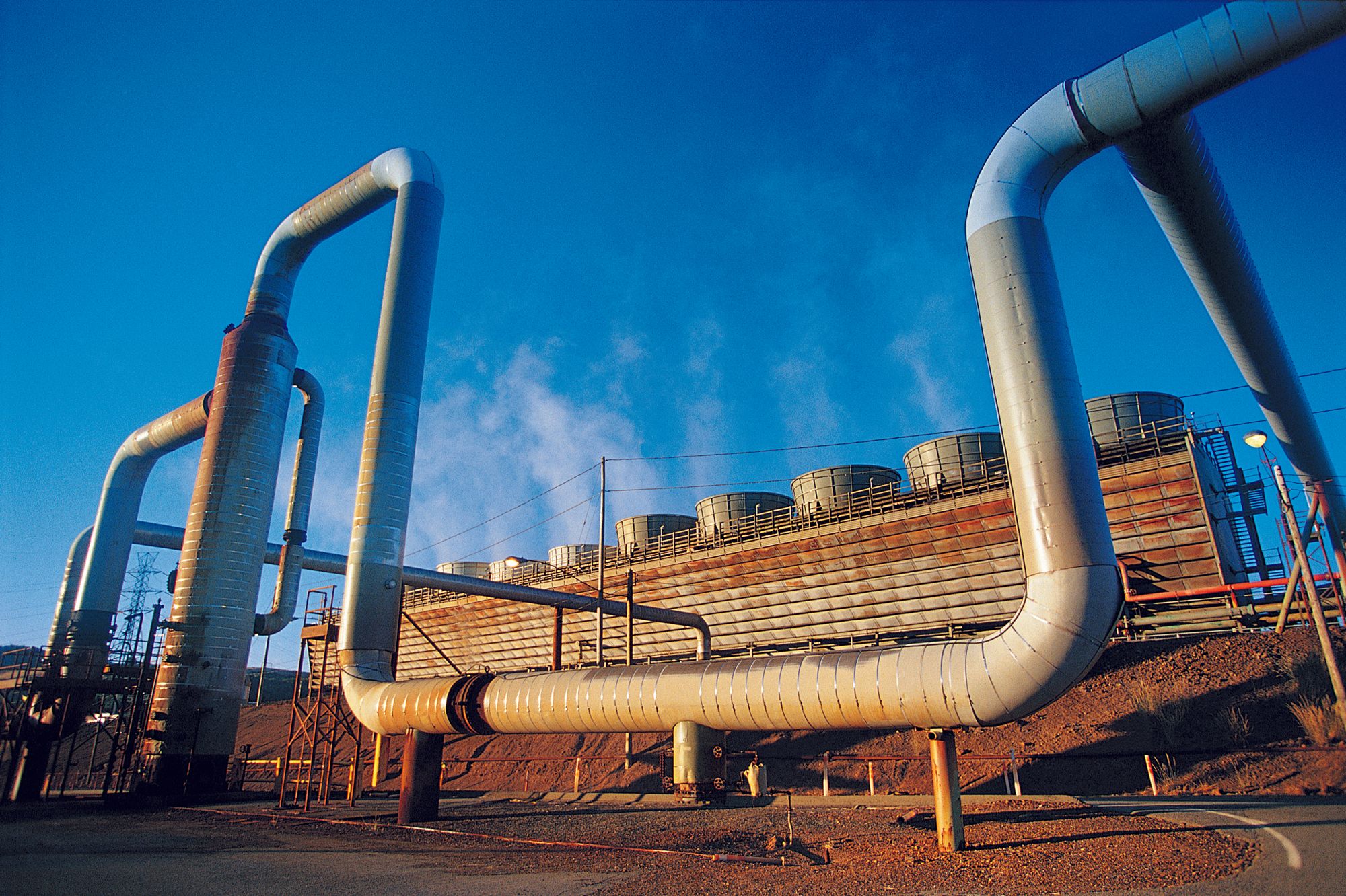
We recently had a comment posted on Tracy Strawn's blog post "Preventive Maintenance - The Cost of Maintaining Equipment"
Khaled Ekram asked the question:
"What if we could identify failure before it happens with a reasonable time in which we could order the damaged parts and recieve it (within the lead time), if we could have a signal or alert for failure or measurment which could give an indication of failure propability we may save a lot of money by ordering within the perfect time.
Yes we may have a risk of not having the parts before the failure then we may face the shut-down and cost of non-availability for the items but we should try to do such in some cases.
Therefore if you could advise about my suggestion I would be appreciated."
Tracy's response was so detailed that we decided to post it as a full blog post so all blog readers benefit.
In theory it’s possible to achieve an environment where what you have described could take place. Let’s summarize:
- inspections (scheduled replacement & condition monitoring) could lead to early detection of incipient failures
- which in turn would allow the MRO storeroom enough lead time to order the materials
- and have delivered on-site so the repair could be made
- before the equipment reaches a state where failure is imminent (potential failure)
- and the storeroom is managed at the lowest quantity and value
The earlier the detection is made the higher the probability the materials can be ordered and delivered on-site and the repair made while incurring minimal damage to the equipment. This in turn would allow a company to have a Maintenance, Repair, & Overhaul (MRO) storeroom with the minimum parts on hand required to operate and maintain the facilities at the lowest cost and minimal risk to plant uptime and asset integrity. In essence, maintenance is trying to create a “pull” where the “signal” is the condition of the equipment. The signal, which could be described as a defect or “incipient failure”, is discovered by the maintenance tech. The maintenance tech raises a work request which prompts the planner/scheduler to begin the planning process. The planning process prompts the storeroom to order the “part” well enough in advance (supply lead time) so that the “part” arrives and is staged to coincide with the appropriate scheduled start date. This is best illustrated by understanding the Potential Failure to Functional Failure Curve (P-F Curve).
To achieve this scenario the following must take place:
Equipment
All maintainable assets in the plant/facility must be identified and documented
- A maintenance strategy is developed for all maintainable assets
- The maintenance strategy is developed using a risk based approach such as reliability centered maintenance (RCM)
- Critical plant spares are identified through the RCM process
- The maintenance strategy should approximate the following:
- 20% unplanned
- 80% planned
- The unplanned activities would consist of the following:
- run to failure on non-critical equipment (no scheduled maintenance)
- unexpected or unseen deterioration of components resulting in failure
- human error causing failure
- The planned maintenance activities should approximate the following (bear in mind the numbers are ballpark):
- 25% predictive, condition monitoring
- 35% statutory or functional testing
- 10% time based or "scheduled replacements"
- 10% design out
- The planned activities listed above are designed to identify incipient failures or prevent the consequence of failures as soon as practically possible
- It assumes the organization understands the various failure patterns (early, constant and wear out) and P-F intervals where they apply
People
- All technicians are trained and competent in their discipline and understand the basic concepts of maintenance management and equipment inspection
- All technicians have the appropriate and up to date tools
- The organization uses planner/schedulers who are competent
- The organization has well trained supervisors with the proper span of control
- Storeroom has trained and appropriate supervision and personnel assigned
- Well trained Reliability Engineer to assist in writing maintenance strategies and facilitating root cause analysis of unexpected or “design out” equipment failures
Process/Procedures
- There is a documented and effective work management process in place integrated with a CMMS with roles and responsibilities
- All maintainable assets have been uploaded to the CMMS equipment register
- The CMMS is well integrated and implemented so that all personnel understand and use effectively
- Master equipment data (including PM routines) has been assigned to each equipment number (tag) in the CMMS
- PM routines (all) have sufficient detail so that technicians can identify what constitutes a defect (in the failure curve) as early as possible
- Storeroom, working with maintenance has identified all A, B, and C spares
A: insurance spares
B: replace parts
C: consumables - Supply chain management and procurement practices are world class to get materials onsite at agreed upon times
- Storeroom working with maintenance has optimized the storeroom and reduced the spares on hand to the absolute minimum through:
- Storeroom optimization process
- Critical Spares identification through RCM
- Early identification of incipient failures through excellent PM execution
- Excellent planning and scheduling
- Supply lead time well understood and…
- Excellent supply chain management and procurement practices
If the above mentioned elements are in place or have been executed it’s conceivable the storeroom could reduce their spares to only insurance spares and consumables. Most all materials e.g. “B items” or replacement parts could be managed by the ”signal” mentioned earlier. This would in effect create a “pull” system that would allow the organization to stock the minimal amount of parts. With an effective supply chain management system consumables can be kept to minimum through a “kanban” system managed by vendors.
As you can see, to achieve this scenario or what some may call “the ideal plant environment” requires a comprehensive and well executed maintenance management approach and strategy. It also requires an organization including Leadership committed to continuous improvement as this will not be achieved overnight.
I am sure I have left out important details but I think I have given you an idea of what’s required to achieve this goal. It’s not easy and it requires a multi-faceted approach with all key members of the organization involved. Maintenance can’t do it on its own and neither can the Storeroom or materials management group. Everyone from plant leadership down to the shop floor must be committed to helping optimize and improve the process as described.
Thank you to Khaled Ekram for commenting our blog!