Maintenance Scheduling: A good early step in the journey to World Class maintenance
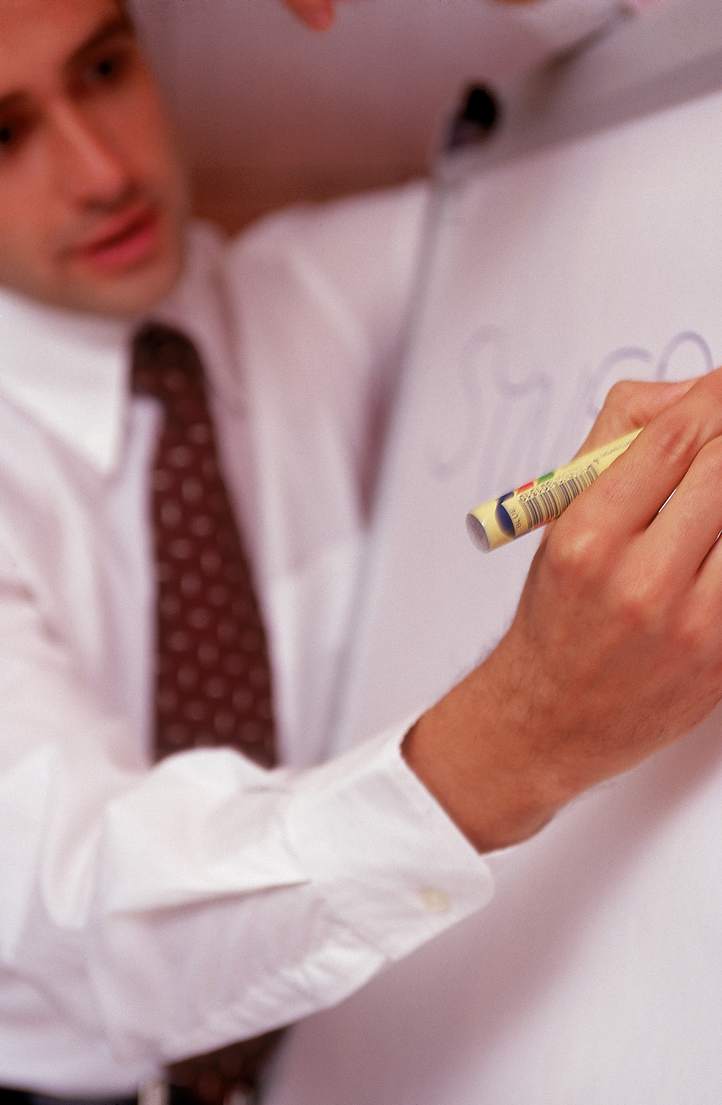
Scheduling maintenance work will yield fast improvements in maintenance productivity. This is achieved by eliminating/reducing several issues that damage productivity in any reactive maintenance organization. Some things required for improvement include:
· Ownership of the schedule by either maintenance or operations
· Equipment locked out and ready for maintenance
· All needed materials available
· Weekly scheduling/Multi week scheduling
· Daily scheduling
Some improvement will be seen regardless of the quality or accuracy of the plan estimates.
How to get started:
· Start by creating a weekly schedule for the next week. At first, it may be a schedule created by maintenance, but must progress to a board consensus as the scheduling process matures.
· Use the due dates on PMs or PPM activities to begin populating a 4 to 5 week schedule. It is important to put PMs/PPM activities on the schedule, allowing enough time for the work to be done and the work order completed before the due date.
· Begin to use specific start dates or target weeks -allowing this date to populate 4 or 5 weeks out. This requires a clear objective priority matrix that is well understood by all.
· Establishe the target using the needs of the site, priority, and availability of material or resources.
The scheduling process
A cross-functional team will meet weekly (Thursday afternoon) to review the list of work. Members of the team should include personnel that will commit for their organization. Key members of the team are operation and maintenance leaders that are knowledgeable of the tasks, capabilities of the mechanic and availability of plant equipment. Personnel from other organizations are welcome to attend – especially if they are interested in a specific work order.
Scheduling principles
Scheduling must be from those work orders flagged “Ready to Schedule”, with a target date falling within the period being scheduled and the appropriate priority.
Equipment availability, resource availability and material availability must be met or the work order will not go on the schedule.
Scheduling tools
Most CMMS’s have a scheduling tool that greatly improves the efficiency and accuracy of the scheduling process. The SAP’s Planning Board is a good example. Good scheduling tools allow capacity leveling as items are added and ensures 100% of available maintenance labor is scheduled.
The members should come to the meeting prepared to make scheduling decisions, having reviewed the proposed schedule prior to the meeting. If this requirement is adhered to, the meeting should last 30-45 minutes.
Transitioning to a multi week schedule
A multi week tentative schedule will soon develop. The goal should be to have tentative schedules out 4 weeks. Best in class scheduling processes use similar targets for the out weeks. Each week, the multi-functional scheduling team will review the tentative schedules and adjust as needed.
· Next week 100%
· Week 2 60%
· Week 3 30%
· Week 4 15%
Scheduling in this manner will keep everyone aware of those tasks in front of them, allowing adjustments, to make the schedule possible. As compliance grows, credibility in the scheduling process will increase, reducing the temptation to go around the schedule.
Daily Scheduling
The Maintenance Supervisor will adjust the weekly schedule, daily, to meet the resources and skills he has available. This is done with agreement from operations. The Maintenance Supervisor should not introduce work that is not part of the weekly schedule.
Adjustments to the next day's schedule will consider the status of the current day's schedule, the availability of adequate resources with the right skills, and availability of the operations equipment. This is a very brief meeting (work discussed by exception only) typically <15 minutes and is a good candidate for a stand up meeting.
The Scheduler’s role, at this point, is to make the schedule represent the decisions made.
A clear indicator of a well scheduled maintenance program is any emergency or urgent work will displace scheduled work and impact schedule compliance. A schedule compliance metric should be tracked and openly displayed in the scheduling meeting room.