The Six "Rules" of ROQ
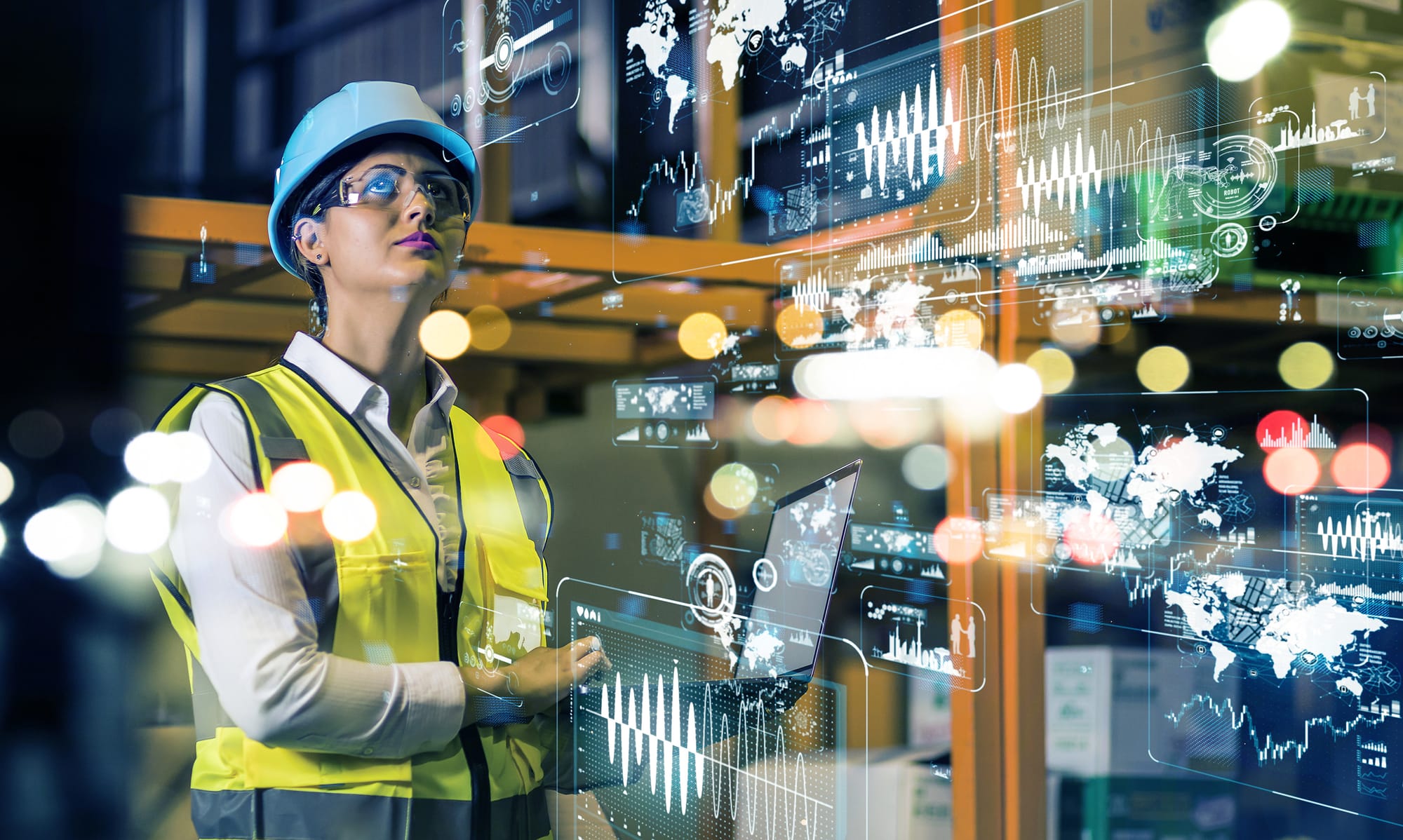
Reorder Quantity (ROQ) is a critical driver in determining the overall inventory value carried in a storeroom. Determining the proper ROQ is crucial and getting it wrong can significantly impact your business. Setting Reorder Quantities too high could lead to a costly stock surplus, while setting them too low may result in excessive orders or stockouts that lead to avoidable equipment downtime. Although much attention (and calculation) is often given to the determination of Reorder Points and Safety Stock levels maintained to prevent a stockout, Reorder Quantities are often determined much more arbitrarily.
For the purpose of this article, Reorder Quantity is defined as the pre-established quantity ordered when the stock level reaches an inventory level that triggers a reorder.
The following six rules can help determine the proper Reorder Quantity. These simple rules serve as guidelines to ensure a ready supply of spare parts, effectively meeting maintenance needs while avoiding the pitfalls of overstock. In this article, we’ll present these rules with examples specific to MRO storeroom operations.

Rule 1: Align ROQ with Vendor Delivery Quantities
The first rule applies specifically to those items that, as a standard, come in predetermined quantities. For example, a bearing supplier may only provide the requested bearing in packs of 10. In cases like this, the ROQ should be in multiples of the standard delivery quantity. For this bearing, orders of 10, 20, or 30 would be appropriate and may allow us to avoid additional fees from the vendor related to delivering partial orders. There is an additional word of caution here: it is very important to understand the unit of measure regarding bundled materials. The mistake of ordering “10 bearings” only to receive 10 packs of 10 bearings is a very easy way to end up with 100 bearings on the shelf.
Rule 2: Meet or Exceed the Vendor's Minimum Order Quantity
The second rule applies to those spare parts that require a minimum quantity to be ordered with every purchase. When this is required, the minimum ROQ should be equal to or greater than the minimum order requirement. For example, if a drive chain vendor mandates a minimum order of 10 feet, your ROQ should align with or exceed this minimum. Ordering below the minimum may be possible but often leads to increased cost per unit.
Rule 3: Embrace EOQ for Predictable Consumption
In cases of predictable and stable consumption patterns, the Economic Order Quantity (EOQ) becomes a valuable tool. EOQ is a formula which utilizes demand rate, carrying costs, and ordering costs to determine the ideal reorder quantity that minimizes overall inventory costs. Imagine your facility's monthly consumption of 500 light bulbs. Through EOQ calculations, you can uncover the most cost-effective reorder quantity, one that balances the cost of ordering and storing the lightbulbs with total value of the quantity ordered to meet demand.
Rule 4: Allow ROQ to Dictate the Frequency of Orders
If EOQ is not utilized, understanding the average rate of consumption at least allows us to select a ROQ that controls the rate at which reorders will be placed. For example, if the average issuance of a stocked HVAC filter is 5 per week, setting a ROQ of 5 would mean we should expect to place an order weekly. If we would rather order monthly, we might select a Reorder Quantity of 20. The goal is to achieve a balance between the total cost of inventory and the total effort involved in placing and receiving orders.
Rule 5: Respect the Shelf Life/Expiry Date
For many components, expiration is not a concern. But for those SKU’s that degrade over time, it is imperative to account for shelf life or expiry dates when calculating your ROQ. Take, for instance, lubricants or greases essential for machinery maintenance. Ensure that your ROQ aligns with the product's shelf life, safeguarding against overordering that leads to wasteful disposal or, even worse, the use of expired components or materials that lead to early equipment failure or costly damage.
Rule 6: Elevate Stock Beyond the Reorder Point
To prevent unexpected stockouts, it is often imperative to ensure the ROQ is enough to, at a minimum, raise your MRO stock level back to a level above the reorder point. For instance, suppose a reorder for filters is prompted when the stock level reaches twenty-five. An order for 20 filters is placed. By the time the order arrives, the stock has plummeted to one. No reason for panic, right? The new order is on the shelf and we have avoided a stockout (for now). However, the new stock level now rests at 21, four units below the reorder point of 25. This may allow the stock level to be depleted to zero without triggering a reorder. If your system or process protects you from this potential pitfall, great! If not, beware and make sure the amount ordered elevated the inventory to a level that will trigger another reorder when appropriate.
The mastery of these six fundamental rules for determining Reorder Quantity is pivotal for efficient MRO inventory management. When executed effectively, these principles allow a strategically achieved balance between maintaining equipment reliability and averting unnecessary inventory costs. Whether storing spare parts for drive chains, bearings, filters, light bulbs, or lubricants within your MRO storeroom, these rules serve as the keys to a cost-effective inventory management system.
Break these rules at your own risk!
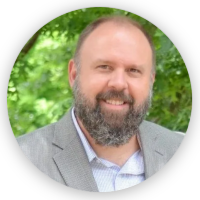
Written by Steve Gowan
Steve is Marshall Institute's VP of Consulting Services.
Reach out to Steve with any follow-up questions, comments, and discussions. Email him at sgowan[at]marshallinstitute.com