Training Snapshot: Maximizing Asset Reliability through Preventive Maintenance
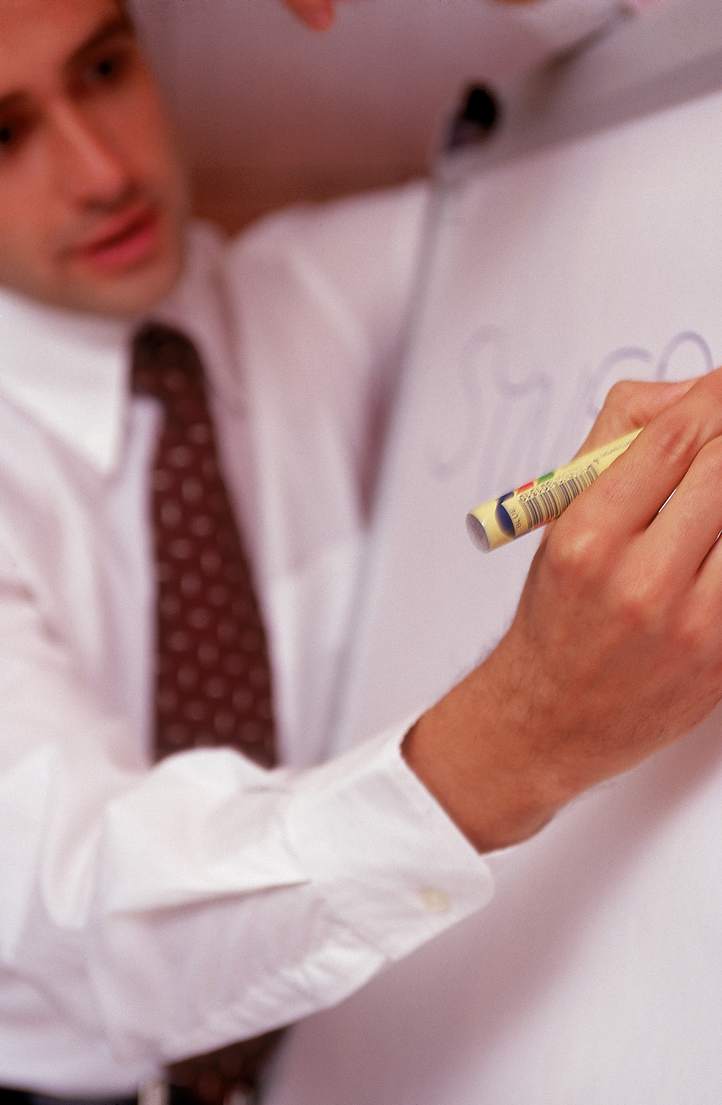
If you have ever wanted to peek under the hood of Marshall Institute’s training content, now is your chance. I will be revealing content from our maintenance and reliability public seminars in this Training Snapshot series. This is the second post in the series. The first post provided a snapshot of our Materials Management for Maintenance seminar.
In this post, we are looking into our Maximizing Asset Reliability through Preventive Maintenance seminar. The content below is taken from the first of seven sections. In this section, we are covering the definitions of preventive maintenance, corrective maintenance, and the typical problems with PMs Today. We wrap up this snapshot with seven questions for YOU to think about. Your answers will be illuminating and the process of collecting this data will be powerful. Enjoy this snapshot.
Preventive Maintenance (PM)
Preventive Maintenance can be defined as any activity that...
- Reduces equipment failures
- Reduces the magnitude of equipment repairs or repair costs
- Reduces product loss or production downtime due to equipment failure or repair
- Reduces deterioration in the productive capacity of equipment
Preventive Maintenance is the application of scheduled work to reduce the frequency and consequence of failure.
We often confuse Preventive Maintenance, Predictive Maintenance, condition-based maintenance, and time-based maintenance. The term “Preventive Maintenance” can imply either conditioned or interval based maintenance. “Predictive Maintenance” is a general term used to describe the higher technology tools such as oil analysis, vibration analysis, etc.
Corrective Maintenance (CM)
Corrective Maintenance is...
- Actions performed as a result of a failure to restore an item to a specified condition
- Maintenance performed to improve equipment and its components so that preventive maintenance can be carried out reliably; e.g. equipment with design weaknesses must be redesigned
“Glossary of Reliability and Maintenance Terms”;
Ted McKenna & Ray Oliverson, 1997, Gulf Publishing
CM from PM
-
PM inspections result in planned corrective maintenance work
-
should not be performed at the time of the inspection
-
both inspections and fixed interval work can be planned and scheduled
-
-
CM work results from PM, Basic Equipment Care, and Root Cause Analysis
-
generally represents an additional 40-45% of the workload
-
more efficient through the use of a planner and job plans
-
Typical Problems with PMs Today
- Inadequate task descriptions
- Too short
- Poorly worded
- Incomplete
- Many PM Tasks are done too often
- Many PM Tasks are done too late
- Duplicate tasks are assigned to multiple people
- Often tasks are “cut and pasted” from similar equipment; PMs are not applicable to that piece of equipment
- Many PMs are simply not value-added; serve no purpose whatever
- Many tasks are too intrusive; may cause more problems than they solve
- Alternative diagnostic tools and technologies not considered, or not being used
- Low PM completion/schedule compliance; low priority
- No accountability for quality PM execution; no follow-up; no audit, or analysis
- No Improvement!
In most cases, it is not unusual to find the potential exists for...
- moving approximately 20%–40% of PMs to condition-based criteria
- eliminating many PMs that are doing nothing useful
- **improving effectiveness and extending frequencies of those that survive
- adding PM/PdM routines that are missing
Discussion Exercise—What’s Wrong with Your PM Program?
-
What percentage of your work orders are breakdown work? ______
-
What is your cost of maintenance? ______________________
-
What is your average overtime percentage? __________________
-
What is your PM schedule compliance percentage? ____________
-
How often do you turn your storeroom inventory? ______________
-
Do you have a dedicated PM crew? ___ Yes ___ No
-
Does production release the equipment to maintenance to perform the PMs? ___ Yes ___ No